折彎無壓痕模具技術(shù)的設計思路全過程
用戶痛點:傳統(tǒng)數(shù)控折彎的缺陷
如圖一所示,傳統(tǒng)折彎所用的凹模為整體式固定凹模。在彎曲力F凸和F的作用下,材料沿凹模V形邊緣移動并受F力的擠壓(如圖二),從而使成型后的零件表面上形成明顯的彎路缺陷,嚴重影響產(chǎn)品的外觀質(zhì)量,圖三中的加粗部分為缺陷帶,其大小=0.414倍于凹模V形槽的寬度。要解決傳統(tǒng)折彎中的上述缺陷,就必須要克服折彎過程中材料的移動和凹模V形槽對材料形成的擠壓力(F凹)。
設計思路:驗證解決方案
2、無壓痕折彎的原理設計針對傳統(tǒng)折彎的缺陷,我們經(jīng)過近兩年時間的充分準備,經(jīng)多種方案的對比論證,利用翹翹板的原理,將折彎凹模設計成可分別繞軸轉(zhuǎn)動的左、右各一件。如圖四所示,模具未工作時,左、右凹模的工作面處于同一水平面。當折彎凸模向下運動進行折彎加工時,左、右凹模分別繞各自的旋轉(zhuǎn)中心作翻轉(zhuǎn)運動,迫使材料在緊貼凹模工作面的情況下繞著凸模的頂點轉(zhuǎn)動,從而產(chǎn)生折彎變形,并最終完成對材料的折彎加工,如圖五、圖六所示。從圖示可知,由于凹模的工作面是轉(zhuǎn)動的,因此通過凹模的工作面而均勻作用到材料表面的力F凹將不會對材料的局部產(chǎn)生擠壓,避免了零件表面因擠壓而形成的摁傷缺陷;同時,由于材料是繞著凸模的頂點進行轉(zhuǎn)動折彎,因此材料在凹模的工作面上也沒有平面滑動,從而避免了零件表面的擦傷缺陷。
敢于實踐:設計折彎無壓痕膜
3、無壓痕折彎模的設計
基于以上原理,根據(jù)客戶現(xiàn)有數(shù)控折彎機的加工能力,我們設計了如圖七所示的模具結(jié)構(gòu)。
根據(jù)客戶板材使用情況,該模具最小折彎材料厚度設計為0.6mm,最大折彎材料厚度鋼板為2mm、鋁板為2.5mm。
在折彎長度的設計上,借鑒數(shù)控折彎機組合凹模的特點組合完成,即圖七所示僅為一個基本單元,考慮到模具加工難度,其長度設計為200mm。工作中可生產(chǎn)多組備用,根據(jù)零件折彎長度的不同要求進行組和。
為保持模具性能的穩(wěn)定和減小模具加工過程中的變形,模座和旋轉(zhuǎn)凹模的材料均選用性能穩(wěn)定的冷沖模專用材料Cr12,且要求必須進行揉鍛加工,碳化物偏析為1~2級(細片珠光體組織)。
采用特別設計的專用拉簧,以滿足模具需要。
該模具符號客戶現(xiàn)有數(shù)控折彎機的各項要求,使用方便、安全、可靠。
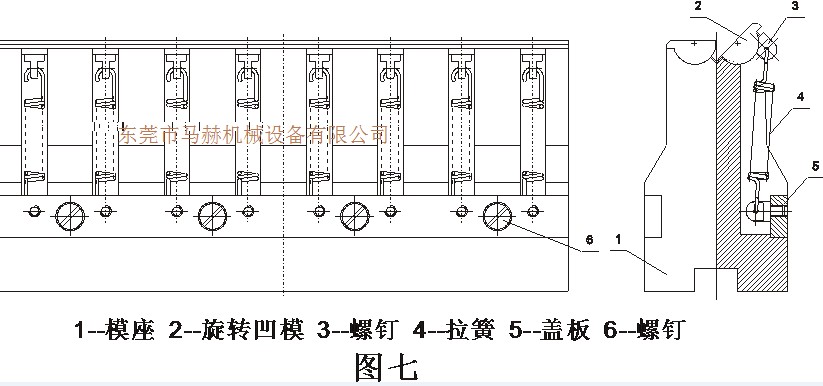
馬赫小編提示:如無折彎無壓痕模具的情況下,短時間的替代方案是使用折彎無壓痕膜,能有效的解決以上的問題。
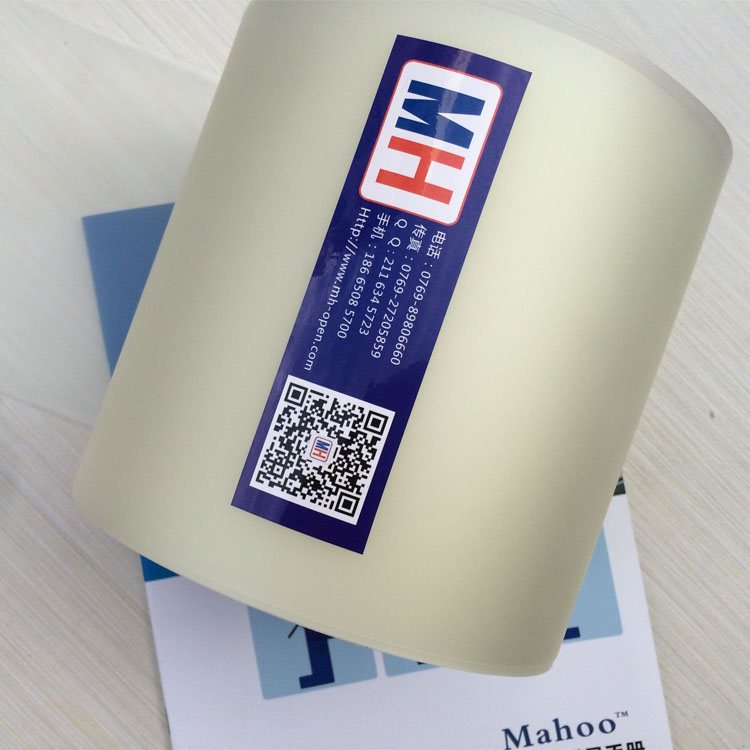